1.简介
我厂安装的是一套高速线材生产线,在粗中轧机之间配有一台飞剪。其工作是否正常,将对生产产生很大的影响。主要功能就是根据工艺的要求,对行进中的轧件进行切头和切尾,并在事故状况下对轧件进行碎断剪切。该飞剪是离合器制动器式,有4片(两对)剪刃,剪刃中心距630mm,宽度180mm。机械装置传动比为7.6:l,由独立的润滑泵供油,最大剪切截面2450mm2,剪切轧件最低温度900℃,剪刃线速度0.8—4.8m/s,轧件速度0.7—4.2m/s,切头尾长度200mm,碎断长度989mm。由一台60kW直流电机驱动,电机最高转速1400rpm。其动作过程为:当控制系统发出剪切命令时,制动器打开,离合器吸合,剪刃离开零位,开始运动,剪切轧件,当剪刃到达停止位时,离合器释放,制动器动作。最后剪刃停止在零位,为下一次剪切作准备。
2.飞剪控制系统的构成
飞剪控制系统原理如图1所示。
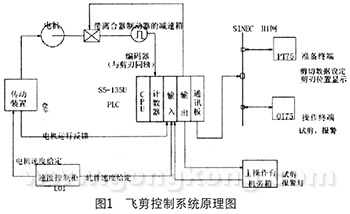
其剪切动作由一台SIEMENS S5-135UPLC控制,上位机与PLC S5—135U之间采用SINEC H1工业以太网连接,主要完成功能:切头,切尾和碎断。
PLC硬件配置:CPU 928B板、高速计数板IP242A,以及一定数量的数字量输入/输出模板,模拟量输入/输出板和SINEC HI通讯卡CPl43。
其中高速计数板在剪刃位置的控制中起到了关键作用。该计数板为一智能模板,可不依赖CPU928B而独立运行,它共有7个计数通道。在系统启动时,通过CPU软件,可根据需要分别设置成不同的计数方式。另外,在其内部还提供了1MHz的计数脉冲,可用于测量每个程序周期的循环时间,进行轧件的跟踪计算。
在剪刃轴上,装有一编码器,用于检测剪刃的实际位置。
机旁操作箱上装有一些测试按钮和信号指示灯,如剪切测试按钮、定位按钮、EMG按钮及信号灯。
通过上位机PT75(准备终端)对剪切参数进行设定,包括切头使能、切头长度、切尾使能、切尾长度、轧件速度修正使能及预设定修正系数。这些数据通过SINEC H1网送到PLC中。另外,有关的剪切状态数据送回显示,如剪切后剪刃的实际停止位和剪切速度。在操作终端OT75相关的显示画面上,可通过颜色的变化来反映飞剪的工作状态是否正常,包括编码器的脉冲计数状态等。还可以点击相应的图标,发出试剪切命令。
3 飞剪控制原理
根据轧件的速度、设定的剪切长度以及飞剪的动作特性数据,控制飞剪的起停。本飞剪为双剪刃,每次剪切,剪刃转过180度。飞剪驱动电机的速度基准由速度控制系统给出,并随轧线一起级联变化。
3.1 轧件的跟踪
经过飞剪的轧件速度是由轧线速度控制系统根据CV50飞剪上游机架电机光电码盘检测到的转速信号,结合该机架的减速箱传动比及轧辊的工作辊径计算得出,经转换通过16位开关量输出、一路频率与速度相关的脉冲信号以及一路0-10V的模拟量信号送往CV50剪切控制PLC系统。在那里可根据需要决定选择使用那个速度基准。这样给系统的组织带来了一定的灵活性,且在某一路信号故障时,可由PLC内部程序判断并自动切换使用另一路信号。通过高速计数器,对其内部提供的1MHz频率的脉冲进行计数,并实时读取计数值,可获得控制程序在每个周期的循环时间,结合修正后的轧件速度,就能得到每个程序循环周期内轧件在飞剪区域的行程。根据飞剪前的热金属检测器HMD的检测信号,就可以对轧件的头尾进行实时跟踪。
3.2 轧件的剪切控制
通过对轧件进行精确跟踪,根据轧线上安装的HMD信号及剪切长度设定值,启动飞剪剪切(见图2)
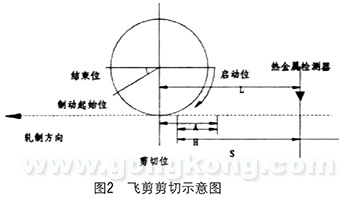
1)当飞剪前的热金属检测器测量到轧件头部信号时,记下此刻的轧件跟踪计数器计数值,以后将该值与轧件计数器值相比较,就能得到轧件头部到HMD的距离S,当S=L-A+H时,开始启动切头动作,制动器离合器线圈得电。其中:L为HMD到剪刃交叉点的距离。A为切头时,剪刃从启动点到交叉点时,轧件所走过的距离(即剪切提前量)。H为设定的切头长度。
2)当HMD检测到轧件尾部信号时,对轧件尾部离开HMD的距离进行跟踪计数(方法同切头)。当计数值S=L-A-T 时,开始启动切尾动作。其中:T为设定的切尾长度。A为切尾提前量。
剪切命令发出后,通过一输出驱动装置,将动作命令分成两部分,首先使制动器电磁阀的线圈得电,断开制动器,经驱动装置上设定的延时后,离合器电磁阀线圈得电,电机驱动剪刃运动,在剪刃交叉位剪切轧件。当剪刃到达制动起始位时,剪切控制输出关闭,经驱动装置,离合器先失电,经延时,制动器失电,制动投入,最后剪刃停在零位,等待下次剪切。
为提高剪切精度,需对每次剪切的提前量A进行实测,即计算在剪切命令发出后,从剪刃零位到剪刃交叉期间,轧件走过的距离。为防止偶然的计数误差带来的影响,可将最近若干次的测量值取平均;同时还要考虑程序运行周期对剪刃交叉点检测造成的误差,并进行补偿。
在切头、切尾时,还需考虑剪刃在停止位的零位偏差。由于每次剪刃的停止后并不一定正好在零位上。这样,在进行头尾剪切计算时,要对相应的剪切提前量A进行修正,以便获得准确的剪切长度。
由于不同轧制速度下,机械装置的惯性不同,停止过程所需的制动距离也就不一样,速度越快,所需的制动角度也就越大。为使剪切后,剪刃能准确停在零位,在切头、切尾时需对制动角度进行测量,即根据剪刃轴上编码器的脉冲计数值,得到从离合器制动器电磁阀线圈断电到剪刃完全停止时剪刃转过的角度,取最近若干次切头、切尾制动中测量的平均值,作为下一次切头、切尾时的制动角。
4 控制功能说明
寻找零位:初始程序启动,零位找寻工作必不可少,由于编码器安装时,其零位脉冲的不确定性,在系统启动后,须确定该编码器的计数零点时剪刃位置与机械零点间的相对偏差,否则无法根据编码器的计数值来获得剪刃的物理位置,也就无法对飞剪进行控制。具体过程为:系统启动后,在机旁操作箱上按下点动开关,使飞剪以点动速度缓慢地旋转两圈以上,然后按下箱内的一个按钮,并至少保持5秒以上(目的是防止意外误操作),然后松开按钮即可。转动两圈主要是检测计数板及编码器工作是否正常。
由于从轧线速度控制系统送来的轧件速度信号,仅是系统根据CV50前一机架电机速度反馈值,结合机械的减速比和轧辊的辊径计算得出,而随着生产的进行,轧辊在
不断磨损,工作辊径的尺寸也在发生变化,计算速度难免与实际轧件速度间存在偏差。为提高剪切精度,有必要对轧件的实际速度进行实测,以便对用于跟踪的轧件速度进行修正。测量方法如下:测量轧件头部从飞剪前HMD到飞剪后HMD(若切头功能投入,则为从剪刃交叉点到飞剪后HMD)的理论计数距离,将它与实际距离相比较,即可得到一速度修正系数。且该测量在每根轧件的头部进行,并对这一系数进行自适应修正:
(N*K+Ki)/(N+1)--->K
其中N为测量次数(设有最大限值),Ki为本次测量值。该功能可在上位机上根据需要选择投用。
值得一提的是它的状态和故障诊断功能,通过CPU的编程接口,配合外部安装在编程器或PC机上的专用诊断软件,可以观察到程序内部与剪切有关的重要状态信号的变化时序,可根据需要编制监测状态的清单(可以是输入输出信号,标志位或计时器的状态),发送到CPU,程序在每个循环的最后,检测这些信号的状态有无发生变化,如有变化,则把其变化后的状态及本周期的时间计数器值依次存入缓冲状态数据块,由CPU送往PC机,在屏幕上显示出来,并存入预先设置的文件中。这一功能对故障的排查很有帮助,特别是那些偶发性的故障。它可以连续监测,在故障发生后,通过打开存储状态变化的文本文件,根据故障发生的时间,检查该时间区段内各检测信号的状态有无异常,以确定故障原因。
5 程序结构
启动块:创建数据块,并将数据拷贝至工作DB-RAM中;计数卡进行初始设置、启动计数器:SINECH1网络的初始化;重计算有关的剪切参数,并拷贝到工作DB-RAM中。
主循环程序:检测电源及相关信号是否正常;对HMD信号及编码器脉冲计数器进行采集处理,测量剪刃位置。实测轧件速度,并对轧线速度控制系统送来的轧件速度信号进行修正。产生剪切命令和事故碎断命令,控制导槽底板和出口挡板的动作。管理信号及数据的输入输出。与上位机、其他PLC之间的通讯处理;剪切循环的状态诊断。
6 使用中出现的问题
在实际运行中,切尾曾出现异常现象,即尾部的剪切长度失控,甚至剪不到轧件尾部。经分析发现是由于热金属检测器HMD到飞剪的距离太小,该距离与飞剪的剪切提前量基本接近,这样即使设定的切尾长度很长,也可能剪不到尾或剪的很短。开始,我们通过提高飞剪电机速度基准来解决,但这样一来,虽然能剪到尾部,却引出另一问题:由于剪切速度与轧件速度不同步,使切头时剪切速度超前,产生额外的剪切负荷,而在切尾时,常把尾部顶弯,对设备造成潜在的危害。后经过修改程序,将启动轧件尾部跟踪的热检由飞剪前HMD0改为前一机架前的HMDl,且将轧件从HMD0到该机架段的行程折算到以CV50前轧件速度行进时轧件走过的距离(即用CV50前两个机架出口速度的比值乘以HMD0到该机架的距离),并把它加到距离L中。修改后,切尾控制正常。
离合器制动器式飞剪一般适合于剪切断面较大、剪切速度不高的场合,其剪切定位精度由于受控制气源、电磁阀、离合器制动器摩擦片的影响较大。当轧件速度发生较大变化时,会对剪切长度产生一定影响,一般要通过几次试剪来解决。
7 结束语
用PLC组成的飞剪控制系统,使用器件少,工作稳定,故障率低,维护方便,在实际生产中有较广泛的应用。